Des enjeux importants autour des granulats
Le béton est un matériau essentiel dans la construction, mais il provoque de nombreuses émissions de carbone et une surconsommation de ressources naturelles. Les granulats constituent la partie la plus importante d’un béton, environ les 2/3 de la masse, et la fabrication de béton représente elle-même environ 40 % de la consommation annuelle de granulats en France. Il s’agit également d’une ressource non renouvelable, de plus en plus difficilement accessible. La région Île-de-France importe près de la moitié des granulats qu’elle consomme, soit environ 13 millions de tonnes par an (livre blanc UNPG) et on estime que cette consommation va encore augmenter. Dans un tel contexte, réussir à fabriquer du béton en économisant les granulats est un enjeu majeur. Actuellement, les bétons déconstruits et transformés en granulats par concassage sont essentiellement traités de deux façons : soit par leur enfouissement, soit par leur recyclage en matériau de remblai pour les terrassements routiers. Pour préserver les ressources naturelles, il semble nécessaire de modifier le traitement actuel des granulats de démolition afin d’en réemployer une part beaucoup plus importante dans le béton de construction. C’est une ressource rare (notamment dans les métropoles), dont l’approvisionnement est coûteux et générateur de nuisances et pollution, et donc un enjeu important. De plus, les granulats de démolition peuvent être de bonne qualité et les traiter en remblai ne semble pas la façon la plus optimale de les valoriser.
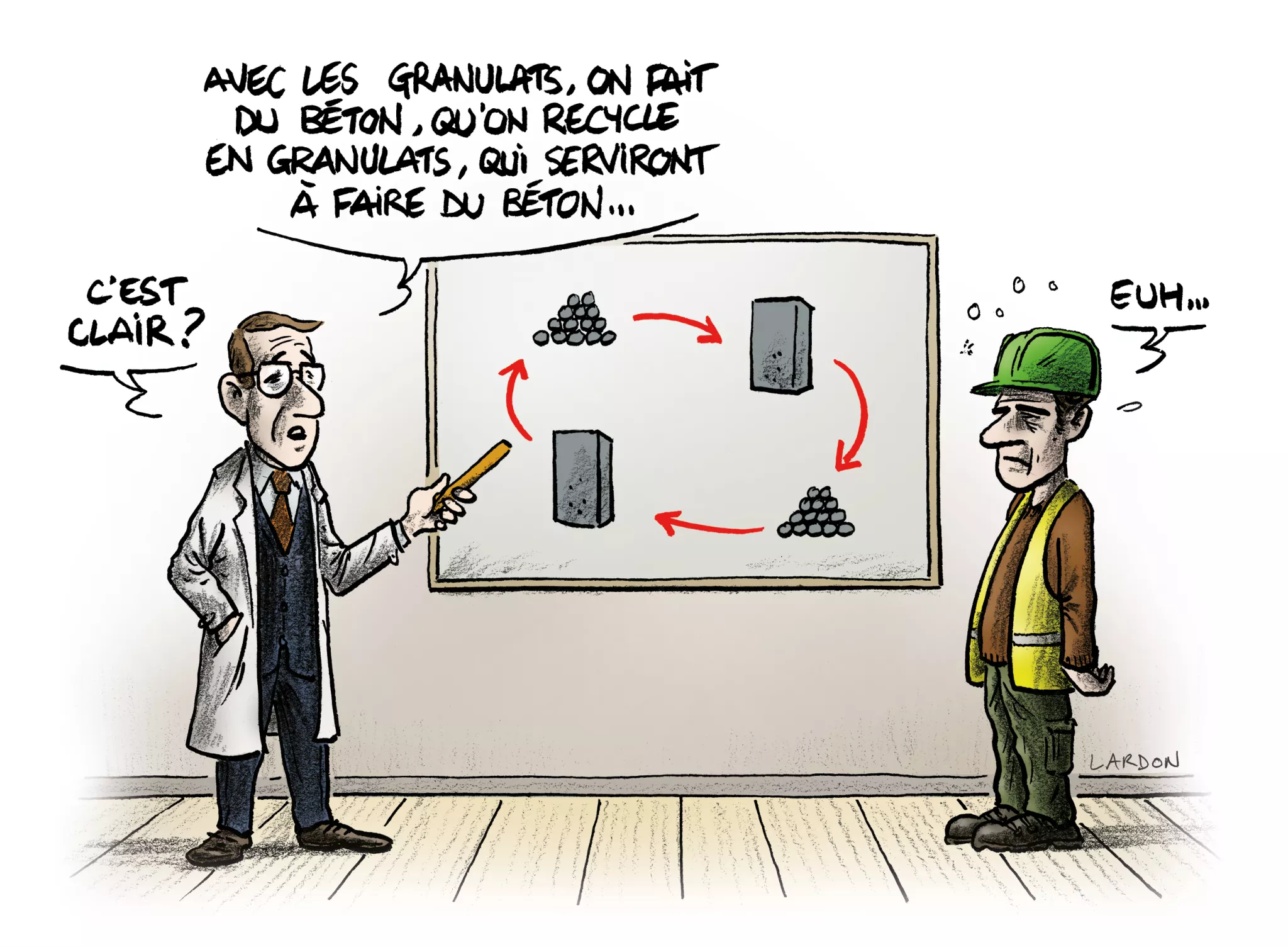
La recarbonatation des granulats de démolition : une voie à explorer
L’usage des granulats recyclés est toutefois ralenti par le fait que ces derniers sont beaucoup plus poreux que les granulats naturels à cause de la pâte de ciment qu’ils contiennent. Mais cette pâte de ciment présente cependant un avantage : elle peut capter du CO2 par carbonatation.
La carbonatation est un processus naturel d’absorption de CO2 au sein du matériau, par formation de calcaire et libération de l’eau contenue dans ces déchets concassés. Cette méthode permet à la fois d’améliorer la qualité des granulats de bétons de déconstruction ainsi que leur bilan environnemental sur le cycle de vie du matériau. En effet, lors de l’étape de fabrication du ciment à partir de calcaire et d’argile, une étape de chauffage de ce mélange permet de « décarbonater » le calcaire ; autrement dit, il émet de grandes quantités de CO2. Plus tard, la réaction d’hydratation engendrée ensuite (entre le ciment produit et l’eau lors de la fabrication du béton) conduit à la formation d’hydrates – des composés chimiques sous forme minérale à l’origine de la résistance mécanique du béton. Cependant, ces composés ne sont pas totalement stables. En présence du CO2 atmosphérique, la carbonatation des hydrates se produit naturellement, et ces derniers se retransforment lentement en calcaire et gel de silice, bouclant ainsi le cycle minéral. Cette réaction est néfaste pendant la phase de service d’une structure en béton armé car le pH du béton, particulièrement élevé initialement, s’abaisse. Cela conduit alors à la corrosion des armatures en acier qui renforcent le béton. Mais, une fois la structure arrivée en fin de vie, cette réaction peut être utilisée comme un atout, notamment dans l’optique de recycler le béton.
Ainsi, ce processus envisagé, dit de « recarbonatation des granulats de démolition », constitue une voie de valorisation qui présente un double avantage environnemental : le piégeage du CO2 d’une part et l’amélioration des propriétés constructives de ces granulats d’autre part. Cela permet de refaire des bétons de meilleure qualité sans rajout de ciment par rapport à un béton de granulats naturels, et ainsi, l’impact CO2 du béton peut être réduit jusqu’à 10 %, par l’utilisation de sables et gravillons recyclés et recarbonatés [1].
Cette valorisation est actuellement permise par la norme mais de façon limitée. Pour cela, et grâce à des coopérations exemplaires entre recherche publique et entreprises, la qualification de cette technologie est essentielle afin d’apporter des éléments d’éclairage aux réflexions autour de l’évolution de la normalisation en cours.
L'expérimentation avec Eiffage autour de l'écoquartier LaVallée
Une expérimentation a été mené dans le cadre d’un partenariat entre Eiffage et l’Université Gustave Eiffel sur le site de l’écoquartier LaVallée. En février 2017, Eiffage Aménagement a en effet été désignée lauréate d’un concours d’opérateurs économiques. L’objectif était de constituer la première Société d’économie mixte à opération unique (Semop) d’aménagement de France, aux côtés de la ville de Châtenay-Malabry (92) et de la Caisse des Dépôts et Consignations. Cette Semop avait pour mission la réalisation de l’écoquartier LaVallée, à Châtenay-Malabry, sur un terrain de 20,6 ha.
La ville ayant de grandes ambitions pour cette opération de renouvellement urbain, Eiffage Aménagement a proposé d’en faire un écoquartier démonstrateur de la ville durable, avec la construction d’immeubles d’habitations (2 200 logements) mais aussi, de 36 500 m2 de bureaux, de 15 000 m2 de commerces, d’une ferme urbaine et d’équipements publics, (crèche, école maternelle, primaire, collège et parking public), le tout associé à des espaces publics paysagers de qualité. De plus, deux objectifs très importants ont été inclus pour la construction de ce quartier : le bas carbone et l’économie circulaire. Dès le début du projet, il s’est agi de mieux maîtriser les conséquences de la construction, par exemple, en s’orientant vers des bétons à l’impact carbone réduit, ou vers le recyclage des bétons démolis en granulats et la recarbonatation de ceux-ci. L’enjeu par le biais de ce projet est donc d’expérimenter pour la première fois en France à grande échelle une technique de recyclage de bétons. Complétant le projet national FastCarb qui a étudié la recarbonatation des granulats de béton recyclé [2][3], du CO2 sous pression fut aussi injecté dans les granulats issus de la déconstruction du chantier de l’écoquartier LaVallée afin de tester leur capacité à piéger du carbone, et ainsi à diminuer leurs répercussions sur l'environnement.
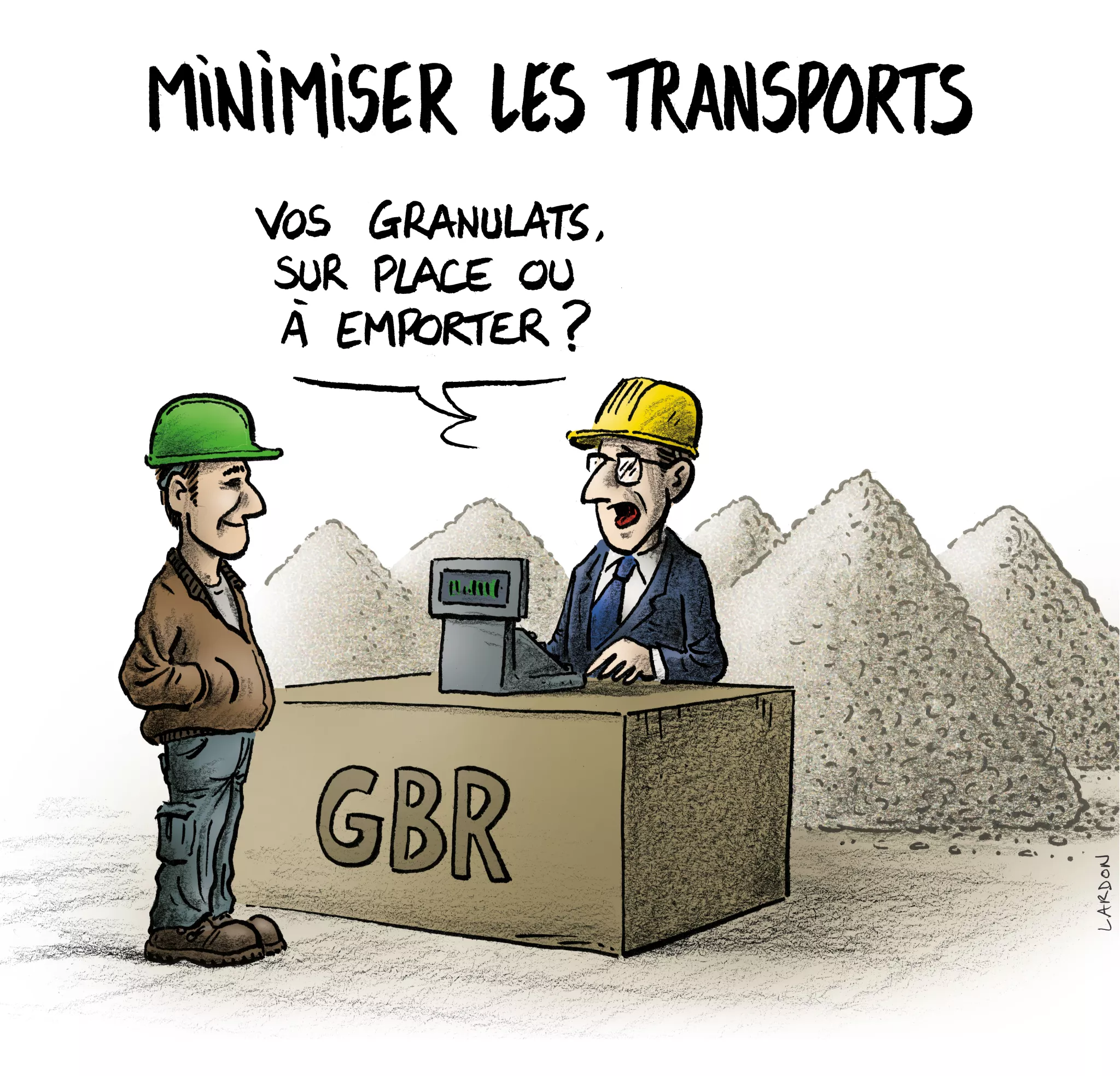
Les résultats de l'expérimentation de l'utilisation de bétons recyclés
Le projet a permis la comparaison de deux bétons incluant des granulats de bétons recyclés (GBR) : l’un avec 20 % de GBR 8/20, soit 12 % de la quantité totale de granulats conformément à ce qui était autorisé par la norme à l’époque, et l’autre avec 100 % de GBR 3/8 et 8/20, correspondant à 51 % de la quantité totale de granulats. Les chiffres indiqués traduisent la taille minimale et maximale du diamètre des granulats en mm, par exemple les GBR 8/20 mesurent ainsi entre 8 et 20 mm de diamètre. Une centrale à béton dédiée au béton de granulats recyclés a été déployée sur site. La production de ce béton, avec 100 % de GBR 8/20, a été limitée pour la conception d’éléments verticaux des derniers étages d’un lot du projet, en raison de performances inférieures et de la nécessité d’une conception adaptée.
Dès sa mise en œuvre, le béton subit des phénomènes physiques, chimiques, thermiques et hydriques qui modifient sa microstructure et génèrent des déformations spontanées – le retrait – qui peuvent l’amener à se fissurer si elles sont gênées. L’utilisation d’une plus grande quantité de GBR dans sa composition engendre quelques conséquences : sa résistance à la compression, sa masse volumique et son niveau de rigidité sont plus faibles, et son retrait, lui, est plus important. Pour remédier à ces problèmes affectant la résistance et la durabilité du matériau, il a été envisagé d’augmenter la part de ciment dans le béton avec GBR, mais cela aurait augmenté sa teneur élevée en carbone et ce choix a été proscrit. Il convient de noter que, pour les deux bétons comparés, le retrait était dans ce cas inférieur à celui prédit par la norme actuelle (EC2-1) pour un béton sans GBR mais avec un niveau de résistance similaire. Et le fluage du béton avec 20 % de GBR 8/20 (c’est-à-dire sa déformation lorsqu’il est soumis à une force externe maintenue et constante dans le temps) est équivalent au fluage d’un béton similaire sans GBR [4].
Le prix des granulats recyclés étant ici inférieur au coût des granulats naturels, cela a permis de réduire le coût des bétons produits de 3 à 5 %. De plus, l’utilisation de granulats recyclés in situ a permis d’éviter environ 6 000 camions qui auraient été nécessaires pour évacuer les gravats et apporter les granulats naturels que l’utilisation de GBR a permis d’économiser. On estime que ce transport évité a permis d’économiser environ 120 t de CO2 et de réduire grandement les nuisances pour les riverains.
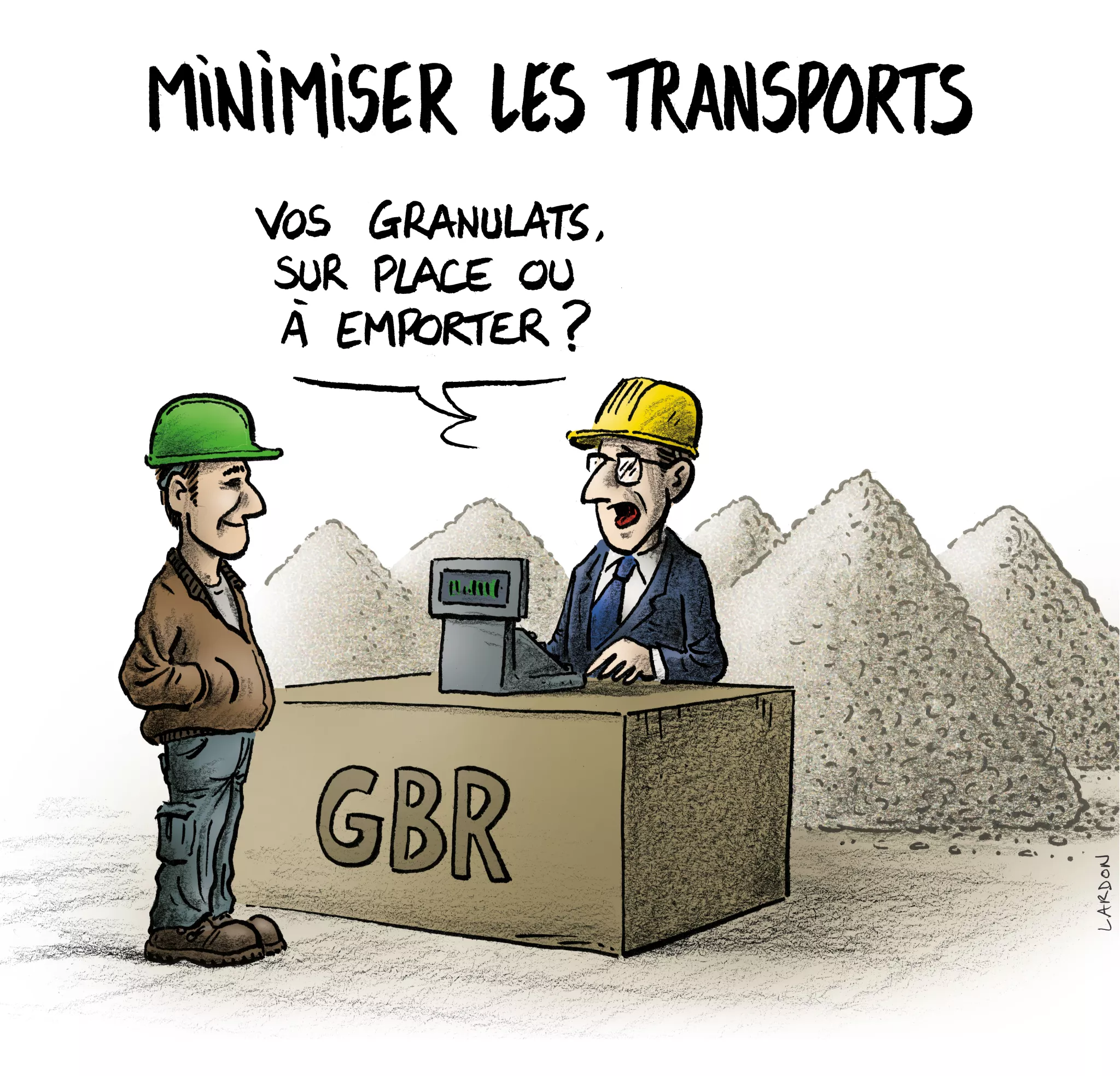
Des paramètres à maîtriser pour optimiser les impacts
Toutefois, pour arriver à ces résultats, il convient de tenir compte d’un certain nombre d’enjeux qui concernent le processus de production des bétons, mais aussi plus largement leur transport et l’organisation des acteurs impliqués. Ces enjeux sont notamment de tester la broyabilité des bétons de déconstruction afin de sélectionner les plus qualitatifs à recycler et d’obtenir un maximum de béton propre dans les gravats triés, mais aussi d’enlever la présence problématique de bois et de plastique pour obtenir des gravats de bonne qualité. À cela, s’ajoutent le fait de pouvoir stocker dans de bonnes conditions les GBR afin d’éviter qu’ils ne soient pollués, notamment par mélange avec le sol, et enfin de réduire les répercussions des transports en mettant en pratique, sur la zone urbaine concernée, la boucle chronologique suivante : démolir l’ouvrage ; traiter les gravats ; stocker les GBR ; (re)construire de nouveaux ouvrages.
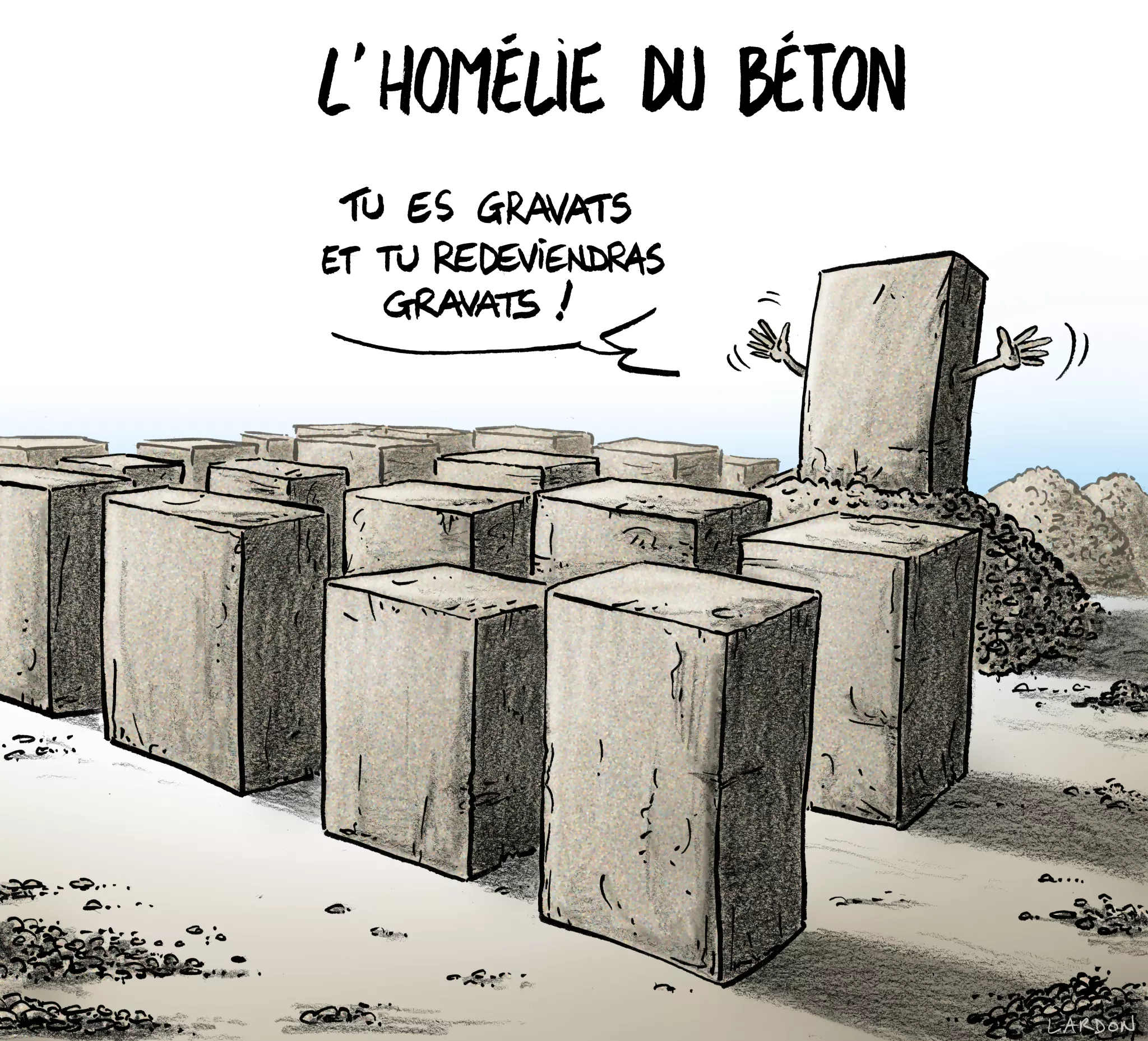
Cette recherche pose également la question de la structuration des filières et des acteurs impliqués. Le traitement des produits de démolition est une activité ponctuelle et diffuse, contrairement aux carrières de granulats naturels. Les flux dépendent alors de la taille et du calendrier des travaux, ainsi que de la nature des chantiers de démolition, mais nécessitent que les acteurs soient prêts à faire face à des flux importants. Il serait par ailleurs souhaitable que la même entité gère à la fois les travaux de démolition et les travaux de construction, car même en déléguant certaines tâches aux entreprises et à leurs sous-traitants, elle aurait alors une vision globale de l’ensemble de la boucle et pourrait optimiser le coût et réduir les répercussions environnementales. Par exemple, elle pourrait accepter un prix plus élevé pour la démolition, s’il est synonyme d’un meilleur tri. Ensuite, elle pourrait imposer d’utiliser les GBR pour les ouvrages en béton.
Conclusions
L’écoquartier LaVallée a ainsi permis de démontrer sur une grande échelle que le recyclage du béton est possible sur un vrai chantier avec des effets bénéfiques : préservation des ressources naturelles et limitation des transports (diminution des nuisances sonores, émissions supplémentaires de CO2 évitées) avec une solution techniquement et économiquement pertinente. Ce résultat a été obtenu grâce à une attention particulière portée à la caractérisation en amont, au nettoyage des gravats de démolition, à un tri minutieux et à un stockage propre.
Bien que non généralisable au regard des paramètres qui jouent sur les résultats, il montre la pertinence des points de vue environnemental et économique d’une solution qui n’était pas évidente avant la construction. Enfin, la recherche menée dans ce cadre a également permis la qualification de la technologie de recarbonatation et apporté des éclairages à la réflexion autour de la normalisation, avec des perspectives principales : d’une part, pour le béton de bâtiment, et d’autre part, pour les pistes d’aéroport (un type de circuit court avec un fort enjeu de sécurité).
Financeurs :
Les études mentionnées ont été conduites dans le cadre de deux projets : le projet national FastCarb (www.fastcarb.fr/), ainsi que dans le cadre du projet de R&D E3S, partenariat entre Eiffage et l’Université Gustave Eiffel (www. programme-e3s.com).